A Comprehensive Guide to the Process and Advantages of Plastic Extrusion
In the substantial world of production, plastic extrusion becomes a crucial and extremely reliable process. Translating raw plastic into constant profiles, it caters to a wide variety of industries with its impressive flexibility. This guide aims to clarify the detailed actions entailed in this technique, the types of plastic appropriate for extrusion, and the game-changing advantages it offers the industry. The following conversation promises to unravel the real-world effects of this transformative procedure.
Understanding the Basics of Plastic Extrusion
While it might show up complex initially glimpse, the procedure of plastic extrusion is essentially basic - plastic extrusion. It is a high-volume production method in which raw plastic is thawed and shaped into a constant account. The procedure starts with the feeding of plastic product, in the form of powders, granules, or pellets, right into a warmed barrel. The plastic is then thawed making use of a combination of warmth and shear, applied by a rotating screw. When the molten plastic reaches the end of the barrel, it is required with a little opening known as a die, shaping it into a preferred form. The designed plastic is then cooled down, strengthened, and reduced into preferred lengths, completing the process.
The Technical Refine of Plastic Extrusion Explained
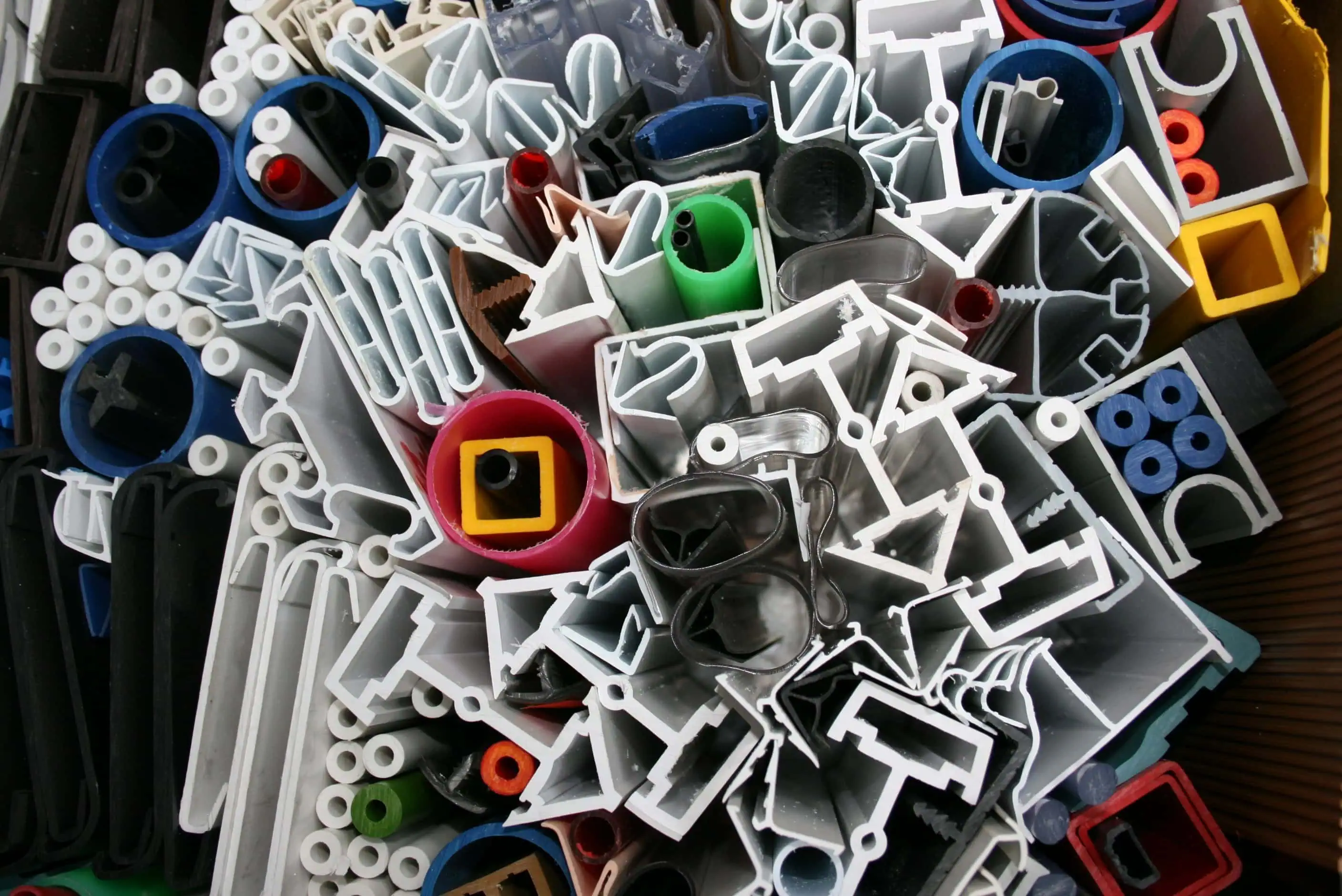
Kinds Of Plastic Suitable for Extrusion
The choice of the right kind of plastic is an important aspect of the extrusion procedure. Various plastics offer distinct properties, making them much more fit to certain applications. Polyethylene, for instance, is generally utilized as a result of its reduced expense and very easy formability. It supplies superb resistance to chemicals and wetness, making it perfect for items like tubing and containers. Polypropylene is another popular choice due to its high melting point and resistance to fatigue. For more durable applications, polystyrene and PVC (polyvinyl chloride) are frequently selected for their stamina and toughness. These are typical choices, the selection ultimately depends on the particular demands of the product being created. So, understanding these plastic types can significantly improve the extrusion process.
Contrasting Plastic Extrusion to Various Other Plastic Forming Techniques
Understanding the types of plastic suitable for extrusion leads the way for a broader discussion on how plastic extrusion piles up against various other plastic forming methods. These include shot molding, strike molding, and thermoforming. Each approach has its one-of-a-kind uses and advantages. Shot molding, for example, is superb for developing elaborate components, while impact molding is excellent for hollow items like containers. Thermoforming excels at forming shallow or large components. Nonetheless, plastic extrusion is unmatched when it pertains to producing constant profiles, such as seals, gaskets, and pipelines. It also enables for a regular cross-section along the size of the product. Hence, the selection of approach mainly relies on the end-product demands and requirements.
Key Advantages of Plastic Extrusion in Production
In the realm of manufacturing, plastic extrusion uses lots of considerable advantages. One notable advantage is the cost-effectiveness of the process, which makes it an economically attractive production approach. Furthermore, this strategy supplies remarkable product flexibility and improved manufacturing rate, consequently raising overall production performance.
Cost-Effective Manufacturing Technique
Plastic extrusion jumps to the leading edge as a cost-effective production technique in manufacturing. In addition, plastic extrusion requires much less energy than conventional manufacturing techniques, adding to reduced functional costs. On the whole, the monetary advantages make plastic extrusion an extremely eye-catching choice in the production sector.

Superior Item Flexibility
Past the cost-effectiveness of plastic extrusion, one more substantial advantage in manufacturing depend on its premium item flexibility. This process permits the production of a vast selection of products with differing dimensions, forms, and styles, from simple plastic sheets to elaborate profiles. The flexibility is credited to the extrusion pass away, which can be customized to generate the wanted item style. This makes plastic extrusion a perfect solution for industries that require tailored plastic parts, such as vehicle, construction, and product packaging. The capability to generate varied products is not only advantageous in conference certain market needs however additionally in allowing manufacturers to discover new product visit with marginal capital expense. Essentially, plastic extrusion's product adaptability promotes development while enhancing functional efficiency.
Improved Production Rate
A considerable advantage of plastic extrusion lies in its boosted production speed. Couple of other production procedures can match the speed of plastic extrusion. Furthermore, the capability to keep consistent high-speed manufacturing without giving up product high quality establishes plastic extrusion apart from various other techniques.
Real-world Applications and Influences of Plastic Extrusion
In the realm of manufacturing, the method of plastic extrusion holds profound value. The financial benefit of plastic extrusion, largely its high-volume and cost-effective outcome, has changed production. The industry is constantly aiming for advancements in recyclable and naturally degradable products, indicating a future where the benefits of plastic extrusion can be preserved without compromising environmental sustainability.
Verdict
Finally, plastic extrusion is a reliable and highly effective approach of transforming basic materials right into diverse products. It offers many advantages over other plastic developing approaches, consisting of cost-effectiveness, high result, very little waste, and layout adaptability. Its impact is profoundly really felt webpage in numerous industries such as building, vehicle, and durable goods, making it a crucial process in today's production landscape.
Digging much deeper right into the technical process of plastic extrusion, it starts with the option of the suitable plastic product. When cooled, the plastic is cut right into the required lengths or injury onto reels if the product is a plastic movie or sheet - plastic extrusion. Comparing Plastic Extrusion to Other Plastic Forming Methods
Comprehending the types of plastic suitable for extrusion paves the means for a broader conversation on exactly how plastic extrusion piles up versus other plastic forming methods. Couple of various other production processes can match the speed of plastic imp source extrusion.